Shop Floor Mistakes You Could Be Making
Shop Floor Mistakes You Could Be Making
Waste is a curse word when it comes to producing high-quality, inexpensive products for customers. Waste from shop floor mistakes eats way at the bottom line, the profit.
The more waste there is, the more the customer pays, both in price and time. If the cost of producing a product has to rise because of waste, and the customer has t o pay a higher price for the product, this causes the customer to look elsewhere for the same product.
Likewise, if waste is contributing to missed deadlines of on-time deliveries, this will also cause a loss in the customer base. You may have the best product in the world but if it's not available for consumers to purchase or the price is too high, profitability will be diminished.
According to MachineMetrics, in their blog "8 Wastes of Lean Manufacturing", "In lean manufacturing, waste is any expense or effort that is expended but which does not transform raw materials into an item the customer is willing to pay for". Let's take a look at where in the shop floor process waste can occur.
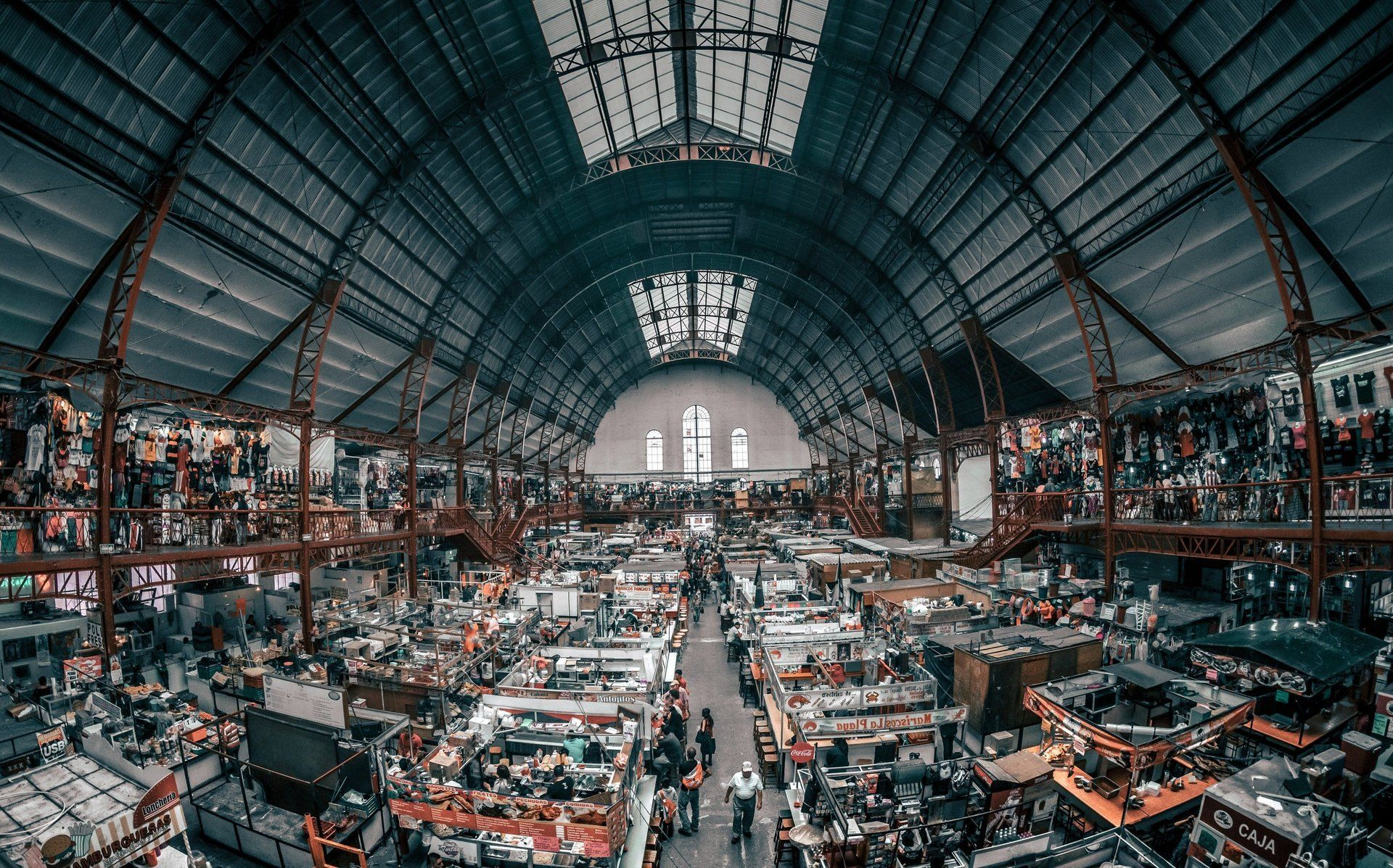
Inventory
According to Investopedia, "Holding costs are those associated with storing inventory. A firm's holding costs include the price of goods damaged or spoiled, as well as that of storage space, labor, and insurance". Inventory on the shop floor can include anything from raw materials, work in progress (WIP) items, and finished products.
When there is a large variance of inventory required to build products, this can lead to miscounting, labor costs, and defects, all waste.
When it takes a long time to build products, (WIP), or there is an overproduction of finished products, those items will linger in inventory over time without generating sales, cutting profitability.
Process Flow
The process flow has to flow seamlessly from one process step to the other until finished products are produced within an on-time delivery deadline.
While developing a product , if a product is designed for function, only, and not for production, wasted labor costs and the inability to meet reasonable on-time deliveries can occur. That's why it's important while designing and developing a product to understand the production process.
For example, item X has 100 pieces to assemble a final product. 5 pieces are to be assembled in process step #1, 90 pieces are to be assembled in process step #2, and 5 pieces are to be assembled in process step #3. Process #1 will assemble the pieces too fast and create a bottleneck for process #2. Process #3 will have idle time waiting for process #2's output. All waste.
Defects
In the production process, defects can occur because of a variety of reasons but two reasons that can be avoided while developing the product are large variances in inventory and poor design and related design documentation changes.
Again, let's say item X has 100 pieces required to assemble a final product and add that item Y also has 100 pieces. All the pieces look the same except with slight variances. It would be easy for an inventory or production worker to mix up the parts and create defective products.
Perhaps, to avoid this, when developing a product, try to require fewer pieces to assemble the products and make them different colors. That way the process is faster and defects are kept to a minimum.
Conclusion
This information just doesn't apply to design engineers but manufacturing engineers as well. To cut waste in every process of the development of a product, from design to quality control to production, can make a difference in big or small profits.
Sometimes, it's beneficial for a team with fresh eyes to see the big picture and ob serve the product development and process to suggest changes that would bring products to market faster, avoid mistakes, and enhance profitability.
Contact us today to see how we can help.