How Finite Element Analysis Will Benefit Your Next Project
How Finite Element Analysis Will Benefit Your Next Project
There’s an increasing demand for streamlined product development, and as a result, there is also growth expected in the area of Finite Element Analysis, reaching 9% CAGR through 2025.
Finite Element Analysis can be a key part of the engineering process and we want to share why.
Finite Element Analysis, Explained: When it comes to a project and how it will respond to predictable effects and forces, Finite Element Analysis (FEA) determines how heat, vibration, compression and tensile loading will affect your project.
First a digital mesh is created using small elements to comprise the design, then mathematical equations are utilized to determine how each element will behave. FEA breaks down larger equations (generally partial differential equations) into simpler algebra, then uses these calculations to predict how the model will respond to different elements. If FEA is used in enough detail, the prediction will accurately reflect actual behavior of the design.
There are several types of FEA. For instance, linear FEA is used when it is assumed that material properties or configurations will not change during the analysis. Non-linear FEA is used for more complex design questions, where the structure and conditions are expected to change under the applied load.
4 Key Benefits of FEA
Here are the benefits you can expect in four areas:
Prototypes: With FEA, fewer physical prototypes are needed. While advances in 3D printing have made developing prototypes significantly more cost-effective, with fewer of them it saves added expenses and material waste is reduced.
Optimization: FEA allows efficiency to be improved in the design process. Performance and design requirements can be met while minimizing materials consumption. FEA pinpoints design failures so that aspects that don’t need additional attention don’t take extra time.
Speed: When developing prototypes, you are tied to the machine shop or manufacturer and their production calendar. With FEA, you may only wait hours to test an updated design, as opposed to days or weeks.
Surprise Costs: FEA helps identify design problems early in the process. Changing parts multiple times causes changes in the tooling and manufacturing process, which can drive up costs unexpectedly at the end of the design process.
At Finite Engineering, our team utilizes Finite Element Analysis to help you predict and understand how a product will react. Contact us to learn more about how FEA can improve your project and reduce costs.
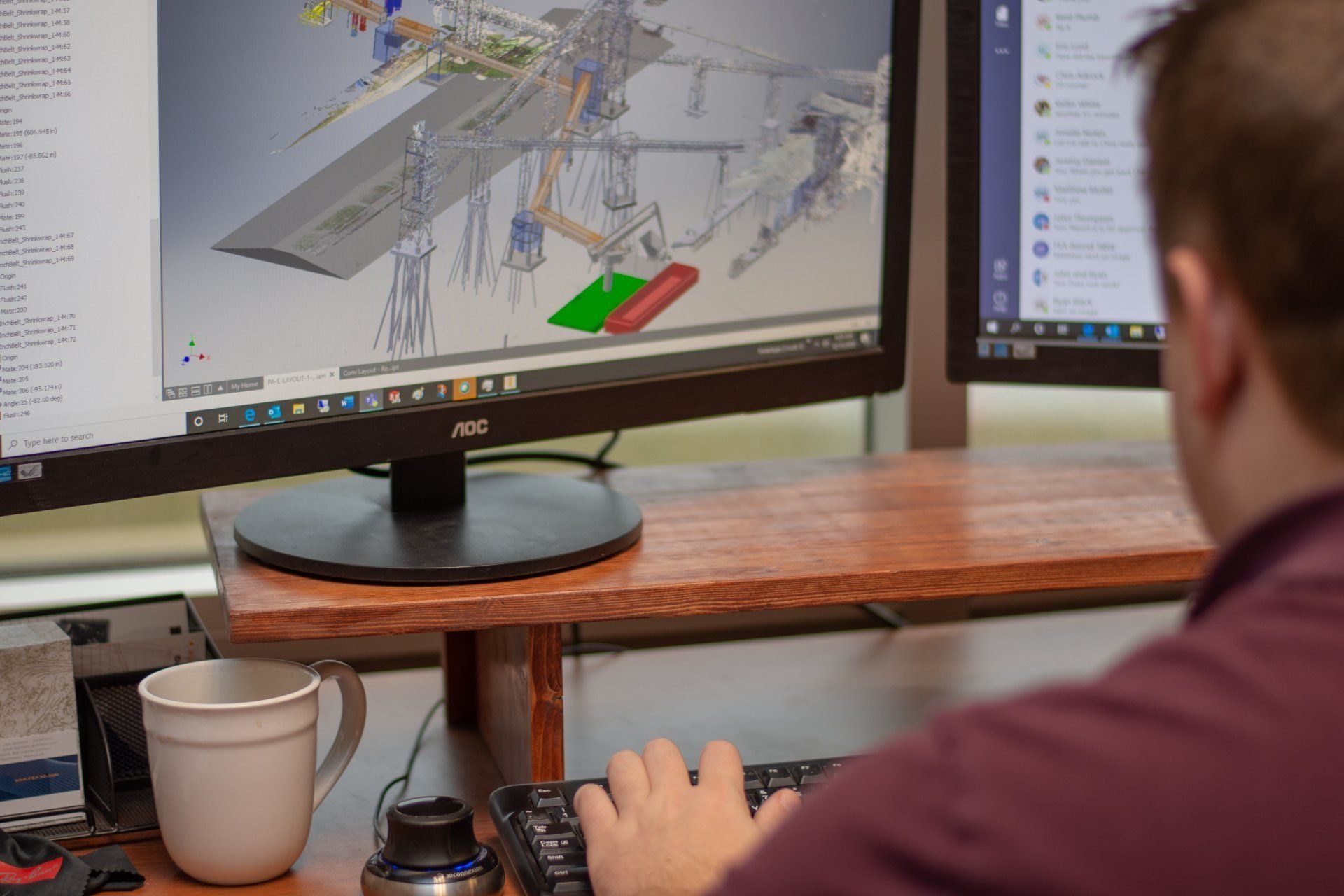